플라즈마 |
1. 플라즈마란 무엇인가 |
|
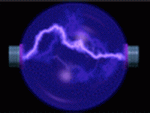
플라즈마 상태는 그 밀도와 온도를 그 주 파라미터로 사용하며 이 두 가지 요소에 따라 우리주변에서도 쉽게 찾아 볼 수 있는 플라즈마 상태들, 즉, 네온사인이나 형광등으로부터 시작하여 북극의 오로라, 태양의 상태, 핵융합로에서의 플라즈마 상태등 광범위하게 분류되어질 수가 있다.
플라즈마라는 용어가 일반인들에게는 생소하게 들릴지는 모르지만 각 가정에서 조명등으로 사용하고 있는 형광등이나, 길거리에서 흔히 볼 수 있는 네온사인, 한 여름에 소나기가 쏟아지면서 자주 발생하는 번갯불과 같은 것들이 플라즈마 상태라고 하면 이해하기가 쉬울 것이다.
이중 공업적으로 이용이 활발한 플라즈마는 저온 글로우 방전 플라즈마로서 반도체 공정에서 플라즈마 식각(Plasma Etch) 및 증착(PECVD: Plasma Enhanced Chemical Vapor Deposition), 금속이나 고분자의 표면처리, 신물질의 합성 등에서 이용되고 있으며, 공정의 미세화, 저온화의 필요성 때문에 플라즈마 공정이 종래의 공정을 대체하고 있으며, 경우에 따라서는 플라즈마 만이 제공할 수 있는 물질이나 환경을 이용하기 위한 응용분야가 점점 더 확대되고 있다
|
|
2. 플라즈마의 정의 |
- 물질의 4번째 상태 |
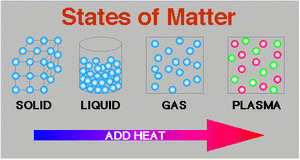
| 플라즈마 속에는 전기적으로 중성인 원자들로만 이루어진 고온 기체와는 달리 서로 반대의 전하를 띤 입자들, 즉 전자와 원자핵이 뒤섞여 존재한다. 따라서 전체적으로는 중성이지만 국부적으로 이온과 전자 사이의 전하 분리에 의해 전기장이, 전하의 흐름에 의해 전류와 자기장이 발생하게 된다. 전기장과 자기장은 보다 넓은 영역에 효력을 미치게 되어 매우 복잡하지만 활용성 또한 높은 물리적 현상이 나타난다. | Fig.1 states of material | |
|
|
- 이온 가스 |
대부분 물질이 고온의 가스 상태에서는 전기적으로 중성 원자들로 구성되어 지지만, 플라즈마 상태에서는 서로 상반된 전해 분자 전자(electrons)와 이온(ions)으로 구성된다. 이 플라즈마 상태에서 전자와 이온이 분리되면 전기장을 만들고 이들 전자와 이온이 이동하면서 전류와 자기장을 생성 시킨다. |
|
- 우주의 99%는 플라즈마로 구성되어 있다. |
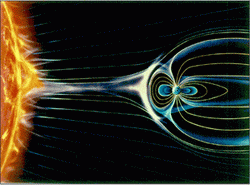
| 지구상에서 플라즈마는 아주 미미하게 발생하지만 전 우주적으로 생각해 보면 전체 우주는 플라즈마 상태가 된다. 예를 들어 태양과 대부분의 별들은 플라즈마로 구성되어 있다. 행성과 행성사이 은하계 공간과 지구의 이온층 또는 전리층이 대표적인 플라즈마의 예이다. 왼쪽 [그림2]은 지구가 태양풍(Solar Wind)이라 불리는 플라즈마의 흐름을 지구의 자기장에 의해서 보호되는 형상을 나타내고 있다. | Fig.2 | |
|
|
좀더 쉬운 예로 플라즈마에 대하여 알아 보자. |
차가운 얼음 조각을 전자 현미경으로 관찰해 보면 각각의 원자가 격자 모양으로 서로 단단히 고정되어 있으며 이것이 고체 상태가 된다. 여기에 약간의 에너지 즉, 열을 가하거나 강한 빛을 쪼여 주게 되면 온도가 상승하고 원자는 격자 상태의 공간에서 움직이기 시작한다. 여기에 에너지를 좀더 가하게 되면 원자들의 움직임이 활발해진다. 이때 고체 상태가 녹으면서 액체 상태로 된다. 이 상태에서 에너지를 더 가하면 원자들 사이가 멀어지면서 사방으로 움직이기 시작하고 액체 상태는 끓기 시작하여 기체 상태가 된다. 위의 3가지 상태 중에는 원자나 분자는 전기적으로 중성이 된다. 즉, 모든 원자는 같은 수의 + 전극(protons)과 -전극(electrons)을 가지고 있다. |
|
|
이 상태에서 좀더 에너지를 가하게 되면 일정 시점에서 빛을 발하기 시작한다. 이때 물질은 더 이상 기체 상태가 아니고 플라즈마 상태로 변하게 된다. 에너지는 중성 원자나 분자를 두개 이상의 전기적 전하 상태로 만들어 버린다. 중성 원자 주의를 돌던 전자는 궤도를 벗어나 이탈하여 자유로운 상태가 된다. 이렇게 생성된 전자들이 점점 증가하여 축적되면 각각 랜덤으로 움직이던것을 멈추고 마치 물고기가 돌고래를 피하기 위해 단체로 움직이는 것처럼 흐르게 된다. 지구상에서는 이러한 플라즈마가 번개나 오로라 형태로 나타나게 된다. 태초의 지구 대기에 있던 번개 형태의 플라즈마가 생물학적 분자 구조를 형성하는 최초의 복잡한 분자구조를 생성했을것이라 여겨지고 있다. | 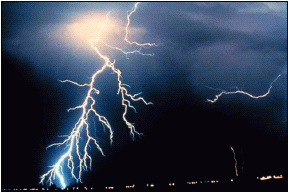
| 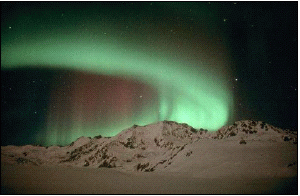
| Fig.3 Plasma example | Fig.4 Plasma example | | |
|
인류가 만들어낸 플라즈마는 여지껏 생성된 가장 강력하고 널리 알려진 기술이다. 플라즈마는 다양한 방법으로 생성되는데 대부분, 컨테니이너 속에 있는 중성 원자에 전자기장력을 복제하여 만든다. |
우리는 형광등이나 네온사인을 켤때마다 플라즈마를 형성한다. 플라즈마는 컴퓨터나 마이크로프로세서의 칩을 만드는데 사용되고 인공관절,제트 터빈날개,플라스틱,금속 막을 씌우는데 사용되고 PDP TV나 철골 건물의 뼈대를 용접하는데 플라즈마 아크가 쓰이기도 한다. 플라즈마가 없었다면 거대 현대 문명을 이룩하는데 이바지하는 IC 가 없었을 것이다. 미래의 플라즈마 응용분야는 값싼 전기에너지를 생산하는 핵융합 반응로나 우주선을 이동시키는 추진력 개발에 쓰일 것이다. |
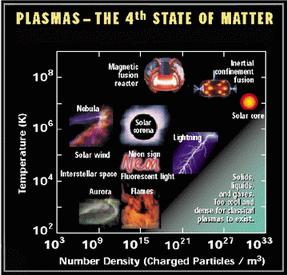
| | Fig.5 | |
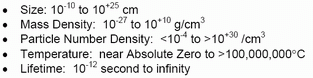 |
|
3.플라즈마 응용분야 |
저온 플라즈마 | 열 플라즈마 | - Dry etching : 플라즈마에 의해 활성화된 라디칼, 전자 등을 이용하여 etching.
- CVD : Plasma를 이용하여 기상합성으로 기능성 막을 생성시키는 방법(주로 반도체 분야의 thin film 형성에 적용함).
- Plasma 중합 : 플라즈마에 모노머를 주입시켜 polimerization을 통하여 기판에 고분자막을 생성시킴.
- 표면개질 : Plasma에 의해 활성화된 이온이나 전자들에 의해 고체 표면을 화학적으로 개질하는 것.
- Sputtering : ion등을 전계로 가속시켜 대상물질에 입사시키면, 대상물질에서 이온 등의 입자가 방출되고 이것들을 기판에 증착 또는 코팅시킴.
| - 플라즈마 용접, 절단 : Plasma의 고온을 이용한 재료의 가공.
- Plasma 용사 : 고융점 분말을 Plasma로 녹여 고체 표면위에 coating시켜 내열, 내식, 내마모성등을 높임.
- 초미립자 제조 : 열플라즈마의 고온,고활성을 이용하여 기상반응으로 합성된 입자를 급냉시켜 초미립자로 합성
- 플라즈마 화학 또는 물리 증착 : 플라즈마를 이용한 기능성 막을 생성
- 열플라즈마 환경기술 : 열플라즈마의 고온, 고활성을 이용하여 폐기물을 분해 및 유리화시킴
- 플라즈마 소결 : 난소결성의 세라믹 등을 단시간에 치밀화시킴
- 플라즈마 야금 : 플라즈마의 고온, 활성을 이용하여 금속을 정련, 제련
| 전자빔이나 글로 방전 플라즈마를 이용하여 공장의 배기가스 중 NOx, SOx를 제거하는 건식 처리기술은 환경분야에서도 플라즈마가 중요히 쓰여짐을 보여준다. 이밖에 최근에는 차세대 고선명 텔레비젼에서 요구되는 대화면(50인치) 평판 표시장치의 하나인 플라즈마 표시장치(Plasma Display Panel)에 대한 연구가 수행되고 있고, 장기적으로는 21세기에 들어 요구되는 에너지, 신재료, 반도체 소자 제조, 환경분야 등에서 플라즈마의 이용이 점점 더 늘어날 전망으로 있으며, 이에 따라 다양한 플라즈마의 생성 및 제어, 측정 기술, 플라즈마의 물성을 측정하는 플라즈마 진단법이 개발이 이루어질 것으로 전망된다 |
|
|
4. 플라즈마의 종류 |
산업적으로 사용되는 플라즈마는 저온 플라즈마와 열 플라즈마로 나눌 수 있는데 저온 플라즈마의 경우 반도체 제조 공정에서 가장 널리 사용되고 있으며, 열 플라즈마는 금속의 절단 등에 응용하고 있다. |
| 저온 플라즈마 (Cold Plasma) | 열 플라즈마 (Thermal Plasma) | 주 발생원 | RF, Microwave, Inductive coupled | DC | 플라즈마 Bulk 온도 | 수십 ~ 수백 ℃ | ~수만 ℃ | 주용도 | 반도체 제조, 형광등 제조 등. | * 고온 (소각, 금속 절단) * 고온 + 화학 반응 (난 분해성 기체 처리, 세라믹 나노 입자 제조 등) | 발생 압력 | ~ 수백 torr | 대기압 | 입자간 온도 | 중성입자 < 이온 ≪ 전자 | 중성입자 ≒ 이온 ≒전자 |
|
|
① 열 플라즈마 |
열플라즈마(Thermal plasma)는 주로 아크 방전에 의해 발생시킨 전자, 이온, 중성입자로 구성된 기체로 구성입자가 1,000-20,000 ℃와 100-2,000 m/s 를 갖는 고속의 젯트 불꽃 형태를 이루고 있다. 이렇게 고온, 고열용량, 고속, 다량의 활성입자를 갖는 열플라즈마의 특성을 이용하여, 재래식 기술에서는 만들 수 없는 다양하고 효율적인 고온 열원이나 물리화학 reactor로 사용되어, 여러 산업분야에서 이용 되고 있다. |
|
열플라즈마의 대표적인 발생법으로서는 직류 또는 교류 Arc 방전을 발생하는 플라즈마 장치와 고주파(Radio Frequency) 자장에 의한 고주파 플라즈마가 주로 이용되고 있다. |
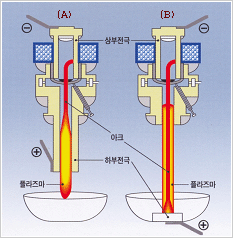
| - 아크방전을 이용한 극간의 직류 또는 교류 아크방전에 의해 기체를 플라즈마화 하는 방법은, 플라즈마를 노즐상의 전극으로부터 고속 고온의 제트로서 분사시키는 플라즈마 토치 형식이 다양하게 고안되어 실용화되어 있다. 1950년대 초기에 현재 사용되고 있는 torch 의 기본적 구조가 거의 확립되었고, 이후 플라즈마 공정의 발전에 큰 공헌을 하고 있다. 가장 일반적인 형태는 제트 방식인 비이송(이행)식 (non-transferred type)으로 텅스텐 음극 봉과 동 양극 노즐 간의 직류 아크 방전을 이용하는 것, 관 형태의 동 전극간의 직류 또는 교류 아크방전을 이용하는 것이 있고, 자계를 인가해서 전극상의 아크 점을 회전 이동시켜서 전극의 손실을 방지하고 부수적으로 플라즈마를 회전시키는 것도 가능하며 메가와트 급의 출력의 토치가 개발되고 있다. 대상물을 양극으로 하며 토치의 음극에서 이것에 직접 아크를 집중하는 방식도 있으며, 이것을 이송(이행)식(transferred type)이라 불린다. 비이송(이행)식 (non-transferred type) 은 주로 열분해 방식의 대기오염 물질처리 분야에서 이송(이행)식(transferred type) 은 주로 열 용합방식의 고형 폐기물처리 분야에 많이 활용되어 지고 있다. | | Fig.6 (A) Non-Transferred Arc Torch (B) Transferred Arc Torch | 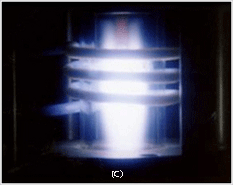
| - 고주파 유도방전은 무전극형이고, 통상 바깥쪽에 코일을 감은 석영관내에 방전부가 존재한다. 코일에 고주파전류를 흘리면, 같은 주기로 변화하는 유도자계와 함께 유도전류가 방전부에 흘러 저항열(주울 열)이 발생해서 열플라즈마 상태가 정상적으로 유지된다. 이러한 고주파 열플라즈마는 유도결합 플라즈마(inductively coupled plasma)라고 하며, 고주파유도 플라즈마를 발생시키는 석영관 토치의 원형은 1960년대 초기에 발표된3) 이후로 그 구조에는 기본적인 변화가 없으나 다양하게 개발되어 현재 정평이 있는 토치가 개발, 시판되고 있다. 최근에 질화붕소관을 이용한 토치도 개발되고 전원도 진공관방식에 더해, 효율 좋은 트렌지스터 방식이 개발되고 있다. | | Fig.7 (C)고주파 유도방전을 이용해서 플라즈마 발생 예 | 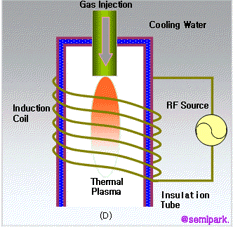
| 고주파 토치로는 축전결합(capacitively coupled)형이 변위 전류에 의한 방전으로 열플라즈마 발생에는 매우 높은 주파수를 요구하기 때문에, 대부분 자기유도 결합형을 사용하고 있다. 유도결합 토치에서는 공기 또는 수냉각 수정관이나 세라믹관 원둘레에 3∼7회 정도의 유도코일을 감아 임피던스 정합회로를 통해 100 kHz∼100 MHz 범위의 고주파 전원에 연결하면, 이때 나타나는 시변 자기장에 의해 유기된 방위각방향 전장이 주입된 기체를 절연파괴 시킨 후 유도코일 전류와는 반대 방향의 원형 전류를 구동하여 방전을 유지시키면서 열플라즈마를 생성한다. 플라즈마의 높은 전기 전도도와 고주파 자기장에 의한 껍질효과(skin effect) 때문에 유도된 전장 분포와 결과적으로 나타나는 Ohmic 저항 가열에 의한 플라즈마 온도 분포는 첨두치가 축에서 벗어나 관 벽쪽으로 치우친 지름방향 분포를 가지고 환단면 껍질(annular shell) 형태의 불꽃을 나타내게 된다. 이는 직류아크 토치에서 볼 수 있었던 축에서 첨두치를 가지면서 지름 및 축방향으로 급격하게 감소하는 물매(gradient)를 가지는 집속된 제트 불꽃 모양과는 두드러진 차이를 나타낸다. 고주파 토치는 직류 아크 토치에 비해 낮은 전력(수∼200 kW)에서 운전하기 때문에 불꽃은 상대적으로 낮은 10,000 K 이하, 100 m/s 이하의 온도와 속도를 갖는 외형적으로 길쭉한 럭비 공 모양의 열플라즈마가 생성되며, 단면적이 직류 플라즈마 제트에 비해 40∼50배로 커서 상대적으로 온도 및 속도 변화 물매가 완만하고, 플라즈마와의 반응물이 비교적 오랫동안 불꽃 속에 머무를 수 있어서 더 많은 운동량과 에너지를 플라즈마로 부터 전달받을 수 있다. | Fig.8 Plasma 생성 | | 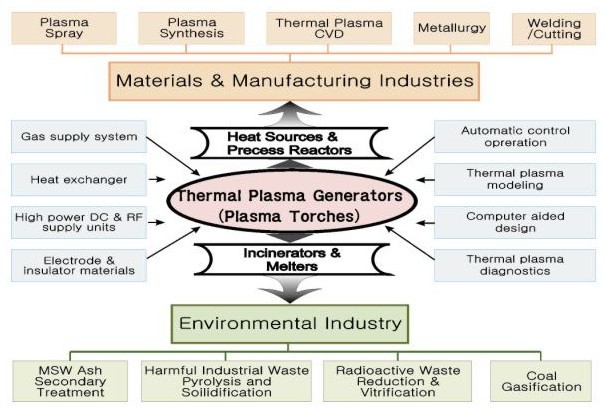
| | Fig.9 |
|
|
② 저온 플라즈마 |
일반적으로 저온 플라즈마는 반도체 제조, 금속 및 세라믹 박막제조, 물질합성 등 다양한 활용성을 가지고 있는데, 대부분 저압에서 생성된다. 상압 비평형 플라즈마는 대기압에서 저온의 플라즈마를 얻음으로써 진공유지, 처리물 장입과 관련된 장치 비용을 줄일 수 있을 뿐만 아니라, 배연가스 처리 및 공기청정과 같이 활용 분야도 더 넓다. 상압 비평형 플라즈마는 펄스 코로나방전과 유전체 장벽방전으로 주로 발생된다. |
|
상압 플라즈마의 발생은 대기압하에서 다양한 방법의 전기방전을 이용하되, 전자 에너지의 세기가 이온 및 중성입자 등의 에너지보다 높게 유지되도록, 즉, 플라즈마가 비평형 상태를 이루도록한다. 전체적인 플라즈마의 온도는 상온~1,000K인데 반해, 전자(electron)의 온도는 10,000 K ~100,000 K가 유지됨으로써 다양한 플라즈마 화학반응 및 표면처리의 응용에 적합한 방전이 가능하다. 상압플라즈마를 구현하는 방법으로는 유전체 장벽 방전 (Dielectric Barrier Discharge,DBD),코로나 방전(corona discharge), 마이크로웨이브 방전(microwave discharge), 아크방전(arcdischage) 등의 기술이 있다. 이 중 수천도의 높은 온도를 수반하여 주로 spray melting 등에 사용하는 아크방전을 제외한 나머지 기술은 모두 비교적 저온에서 구현이 되므로 폴리머 분야나 전자/반도체 공정에 사용이 가능하며, 현재 널리 그 가능성이 타진되거나 적용이 이미 되고 있다. 이 중 유전체 장벽 방전은 기존의 진공플라즈마에 비해 100~1000배 이상 높은 반응활성종(radical)의 농도를 구현할 수 있으면서도 온도가 상온~150℃로 낮아서 폴리머, glass 및 저융점 금속의 표면처리에 적합하다. |
|
응용분야별 저온 플라즈마 분류 |
|
대기압 플라즈마 |
정의 | 기체의 압력을 100 Torr 부터 대기압(760 Torr) 이상 까지 유지하면서 저온 플라즈마를 발생하는 기술을 의미한다. | 특징 | 대기압 플라즈마 시스템의 특징은 화학적 라디칼 생성에서 다른 종류의 발생방식보다 월등히 높은 효율을 나타낸다. | 구분 | 대기압 플라즈마 시스템은 발생방식에 따라 DBD(Dielectric Barrier Discharge)방전 시스템, capillary 방전, Micro-discharge 시스템, RF&MF 대기압 방전 시스템, μ-wave 방전 시스템, Induction & DC Torch 시스템 등으로 구분된다. | 응용분야 | 대기압 플라즈마 시스템은 고가의 진공 장비를 필요로 하지 않기 때문에 경제적이며 펌핑(pumping) 시간이 없고, 인라인 형태로 공정이 가능하므로 생산성을 극대화할 수 있는 플라즈마 시스템을 개발 할 수 있다. 대기압 플라즈마 시스템을 사용하는 응용분야로는 초고속 에칭& 코팅기술, 반도체 패키징, 디스플레이, 물질의 표면 개질 및 코팅 그리고 나노분말 생성, 유해가스 제거 및 산화성 기체의 생성 등 여러 응용분야가 있다.적용기술 | 적용 분야 | 물질의 표면 개질(reforming) 및 코팅 기술 | - 반도체 후공정을 위한 표면 개질 기술 - 표면 친수성 개선 기술 | 환경 기술 | - 환경오염 가스 제거 기술 - 상 · 하수 처리 시 유해물질 제거 및 소독 - 이산화탄소 저감 기술 | 디스플레이 기술 | - 디스플레이 평판 세척공정 - 디스플레이 평판 PR rework 공정 - 디스플레이 평판 PR 에싱(ashing) - LCD용 광원 기술 - 플라즈마 판넬 디스플레이(PDP) | 나노기술 | - 금속 나노 분말제조 공정 기술 - 탄소 나노 튜브 제조공정 |
|
|
|
진공 플라즈마 |
정의 | 기체의 압력을 100 Torr 이하로 유지하여 저온 플라즈마를 발생시키는 시스템기술을 의미한다. | 특징 | 진공 플라즈마의 특징은 정상 상태의 안정한 Glow Discharge 상태를 유지하여 모재(Materials)에 하전입자의 손상을 최소화하며 공정을 수행한다. | 구분 | 진공 플라즈마는 발생방식에 따라 CCP(Capacitively Coupled Plasma) 시스템, ICP(Inductively Coupled Plasma) 시스템, ECR(Electron Cyclotron Resonance) 플라즈마 시스템, SWP(Surface Wave Plasma) 시스템, Helicon Wave 플라즈마 시스템, e-beam 플라즈마 시스템, Pulsed DC 시스템, 이중 주파수(Dual Frequency) 를 이용한 CCP 시스템 등으로 구분된다. | 응용분야 | 100 Torr 이하의 기체 압력에서 작동되는 플라즈마 시스템을 의미한다. 진공 플라즈마 시스템을 이용하는 응용분야로는 일반 반도체 공정에서 사용되는 건식 식각 공정, 증착 공정, 에싱(ashing) 공정, ALD(Atomic Layer Deposition) 등이며 display panel 제조공정, 탄소나노 튜브(CNT)의 성장 등의 공정에서 사용된다.적용기술 | 적용 분야 | 반도체 기술 | - 건식 식각 장비기술 - 박막 증착 장비기술 - 반도체 PR 에싱(ashing) 장비 기술 | 디스플레이 기술 | - 디스플레이 평판 식각장비 기술 - 디스플레이 평판 박막증착 장비 기술 | Nano 및 Bio 기술 | - ALD(Atomic Layer Deposition) 성장 기술 - 탄소나노튜브 성장기술 - 의료용 멸균 기술 |
|
|
|
차세대 플라즈마 |
정의 | 위에서 설명된 플라즈마 발생 기술이외에 신개념 저온 플라즈마 발생 시스템 및 차세대 신기술에 사용될 수 있는 플라즈마를 이용한 시스템을 의미한다. | 특징 | 산업체에서 요구되는 특성을 갖는 신개념 플라즈마 방식으로 예를 들면 중성입자 빔 소스 시스템은 플라즈마를 가속하여 도체의 표면 혹은 중성입자와의 충돌에서 플라즈마 중에서 이온을 고 에너지 중성 입자로 변환시키는 기술로써 기존의 저온 플라즈마 시스템의 문제점을 근본적으로 해결하는 기술로써 개발이 요구된다. 그 밖에 기존의 저온 플라즈마보다 더 낮은 온도의 극저온 플라즈마 발생 시스템의 기술도 범주에 포함된다. | 구분 | 중성입자 빔(Hyper-Thermal Neutral Beam) 시스템, UV-Assisted 플라즈마 시스템, 100kHz MF(middle Frequency) ICP 시스템 등이 있다. | 응용분야 | 중성입자 빔의 응용분야로는 차세대 반도체 공정에서 나노 스케일 반도체 식각 장비, 나노 스케일 증착 공정 및 나노 스케일 리소그래피(Lithography) 공정에서 사용되며 양질의 탄소 나노 튜브 성장 공정에서도 사용될 수 있다. 강력한 EUV를 내는 광소스는 리소그래피에 사용되며 전자빔, 이온빔과 같은 전하입자 빔은 핵융합, 환경산업 등에 사용되고 있으며, 또한 기존의 플라즈마 소스의 약점을 극복하여 새로운 개념의 플라즈마 소스로 대체하는 기술이다.적용기술 | 적용 분야 | 반도체 및 Nano 기술 | - 하전 손상(Charge Damage)이 없는 0.1 마이크론 이하의 선폭 식각 기술 - 50nm 이하의 선폭 리소그래피 기술 - 나노 스케일 초미세 박막 증착 기술 - 저온 탄소 나노튜브성장 기술 - Organic 기판에 상온 박막 증착 기술 | 핵융합 및 환경기술 | - 고온 플라즈마를 위한 중성입자 빔 heating 시스템 기술 - 전자빔에 의한 하폐수 처리 기술 | Bio 기술 분야 | - Biological structure 규명 - DNA 합성 |
|
|
|
반도체 공정 플라즈마 |
|
플라즈마 에싱(ashing) |
플라스마를 이용한 에싱 공정은 Irving이 1968년 Kodak PR 세미나에서 가능성을 제시한 이후 널리 이용되기 시작하였다. 이것은 반도체 제조공정에서 종래 사용되어 왔던 화공약품 (H2SO4/H2O2 또는 알칼리용액)을 사용하는 습식 제거 방법의 단점 (막대한 화공약품을 사용함으로 인한 경제적 부담, 폐수처리 등의 환경문제, 비효율성과 이온주입을 받은 PR은 습식 방법으로 제거곤란)을 해결하기 위하여 제안되었으며, 화학적 에칭과 같은 원리를 이용한다.
초기의 에싱장비는 배치식(100매/배치) 처리를 위하여 원통형의 챔버 구조를 갖고 있었다. PR은 C, H, O의 원자들로 구성되어있는 폴리머이므로 에싱 공정에서는 주로 O2 가스를 사용하여 CO, CO2 등의 휘발성 반응생성물 생성을 통해 제거된다. 이러한 에싱공정은 여러 가지 단점들을 갖고있다. 이중 가장 커다란 문제는 전하축적 손상이다. 에싱 중 일부의 축적전하 전류가 얇아진 PR을 뚫고, 하지 도체 막에 전달되어 쌓이면 그 밑에 있는 게이트 산화막을 파괴할 수 있다. 또한, PR없이 웨이퍼가 플라스마에 노출되면 에싱으로부터 더 심각한 손상을 받을 수 있다.
또 하나의 문제점은 PR속에 미량으로 함유된 중금속 등이 플라스마 에싱으로는 제거할 수 없어 에싱 후 남게 되므로 후속공정에서 하지막으로 확산되어 디바이스의 특성을 저하시키기도 한다. 이러한 문제들을 해결하기 위해 PR 제거공정은 100 % 플라스마 에싱 공정만으로 구성되지 않고, 플라스마 에싱과 습식방법을 9:1 정도의 비율로 적용, 잔유물을 완전히 제거한다. 최근 들어 디바이스 고집적화 (submicron device)로 게이트 산화막의 두께가 6 nm 이하로 줄어들어, 플라스마 손상은 디바이스의 신뢰성을 저하시키는 중요문제로 다시 부각되고 있다.
플라스마 에싱이 공정의 가장 후반 공정이므로 웨이퍼가 플라스마에 직접 노출되어 가장 심각한 손상을 야기시킨다. 보통 플라스마에 의한 손상은 PR없이 플라스마 노출시간을 증가시키는 방법으로 평가하였으나,최근에는 금속전극 상단에 있는 PR이 전하축적을 일으켜 얇은 게이트 산화막을 열화시킨다는 보고가 있어,이에 대한 측정 방법으로 금속-안테나 구조를 이용, 전하축적에 의한 산화막의 파괴특성을 평가하는 것이 일반화되고 있다 |
|
플라즈마 CVD |
얇은 박막들은 현 VLSI회로 제조 공정에서 디바이스 내에서 도체, 금속배선 사이의 전기적 절연체 또는 주변과의 고립을 위하여 널리 사용되고 있다. 이런 얇은 박막에 요구되는 조건들은 다음과 같다. 막 두께는 디바이스 전체뿐만 아니라 웨이퍼간에도 균일해야 하며, 박막의 구조와 조성은 재현성이 있어야 한다. 끝으로 박막증착방법은 안정성, 재현성, 쉬운 자동화와 가격경쟁력이 있어야한다. 가장 널리 사용되고있는 물질은 폴리 실리콘, 산화막, 질화막 등이 있다. 이러한 박막을 생성하는 방법들은 크게 APCVD(Atmospheric Pressure CVD), LPCVD(Low-Pressure CVD), 그리고 PECVD(Plasma-Enhanced CVD) 등이 있다. |
| Methods | Deposition Propertities | APCVD | LPCVD | PECVD | Temperature | 300 - 500 ℃ | 500 - 900 ℃ | 100 - 350 ℃ | Materials | SiO2 ,P-glass | Poly-si SiO2 P-glass Si3N4 | SiO, SiN | Uses | Passivation, Insulation | Passivation, Insulation, Gate metal | Passivation, Insulation | Throughput | High | High | Low | Step coverage | Poor | Conformal | Poor | Particles | Many | Few | Many | Film Properties | Good | Excellent | Poor | Low temperature | Yes | No | Yes |
|
|
PECVD 공정은 플라스마 에칭이 사용되기 이전부터 반도체 금속배선의 보호막인 SiN과 SiO2를 저온에서 증착할 수 있는 새로운 생성원으로 소개되었다. 1975년 TI, AMT사의 상용화된 PECVD 장치가 발표된 후, 1980년에 들어서는 필수적인 반도체 공정설비로 자리를 굳혔다. 이렇게 도입된 PECVD 기술은 SiN과 SiO2 박막형성뿐만 아니라 최근에는 천이금속이나 천이금속 실리사이드형성에서도 널리 사용되고 있다.
PECVD에 의한 박막형성 메커니즘은 . 플라스마에서 이온과 라디칼 형성 . 라디칼 흡착 . 표면에 붙은 원자의 재 분포의 화학적, 물리적 반응들로 이루어진다.
전형적인 PECVD 조건에서는 전자의 에너지가 충분히 작아 이온화 속도보다 라디칼의 형성속도가 빠르다. 또한 라디칼은 높은 흡착계수를 갖고 있어 쉽게 표면에 흡착한 후, 가장 안정된 site를 찾아 이동, 새로운 결합을 만들어 박막을 형성하게 된다. 때로는 외부 공정 변수에 따라 가스상태에서 핵 형성 반응이 일어나기도 하고, 플라스마내의 불순물은 핵 site로 작용, 불필요한 먼지 입자를 생성시킬 수도 있다. 일반적으로 PECVD 공정변수들은 기판온도, 가스조성비, 가스유량, 압력, 입력 파워 및 고 주파수와 전극 간격 등이다. |
|
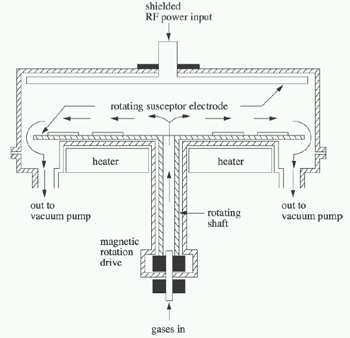
| 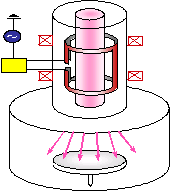
| Fig.10 Action Chamber | Fig.11 | 전형적인 PECVD 장치는 [그림10]와 같이 평형 평판형 구조를 갖고 있으며, 웨이퍼는 접지 전극에 두어 이온 충돌에 의한 스퍼터링 효과를 최소화시키고 있다. PECVD에 의한 박막특성은 증착속도, 박막조성비, 밀도, 굴절률, 막 두께의 균일도, 응력, 표면 Stepcoverage과 에칭속도 등으로 평가한다. PECVD 방식으로 형성할 수 있는 여러 가지 박막들을 플라스마 공정관점에서 구체적으로 살펴보면 다음과 같다. |
|
|
⊙ PECVD SiN, SiO2 박막 |
PECVD를 이용한 SiN, SiO2 박막 형성은 좋은 접합성, 적은 동공(pinhole)밀도, 좋은 표면 덮음율, 좋은 전기적 특성, 저온 증착 가능성과 높은 증착 속도를 갖고 있어 비교적 낮은 용융점을 갖고있는 금속의 보호막 및 다중금속배선간의 공간 절연막으로 사용된다. PECVD에 의한 SiN 박막은 N2/SiH4 또는 NH3/SiH4 혼합가스를 이용한다. 공정변수인 입력 파워를 증가시키면 전자와 라디칼의 밀도가 증가하여 증착 속도는 빨라지고, 압력을 줄이면 라디칼의 확산속도와 전자에너지를 활성종에 전달하는 효율 증가로 웨이퍼간 균일도 향상과 표면에서의 반응이 좋아진다. 또한, 아르곤(Ar)과 같은 비활성 가스를 첨가해 주면 페닝효과에 의해 전자 에너지는 쉽게 라디칼에 흡수되어 균일도가 더 향상된다.
SiN박막의 화학적 결합은 IR-분광기를 이용하여 분석할 수 있는데, 통상 Si-N, N-H, Si-H, Si-O 등이 검출된다. 여기서 Si-O 결합은 반응 쳄버 내의 수분이나 쳄버 벽면에서 이탈된 산소에 의해 생성되므로 증착 전 쳄버를 고온으로 가열시키는 게 필수적이다. Si-H/N-H 결합 비율은 NH3/SiH4 가스조성비에 의해 결정되고, 이것은 박막의 굴절률을 결정하는 중요 변수가 된다. 화학양론(stoichiometric) 관점에서 SiN 박막조성비는 입력 파워, 기판온도, 가스혼합비에 의해 결정된다. 이 박막조성비는 박막의 응력을 결정하는데, SiN 박막은 압축 응력(compressive stress)을 갖고 있어 후속 열처리공정에서 균열과 같은 문제를 유발할 수도 있다.
SiO2 박막은 SiH4/N2O 혼합가스를 이용하여 생성할 수 있다. 여기서 O2 대신 N2O 가스를 사용하는 이유는 N-N 결합 에너지는 N-O 결합 에너지보다 크기 때문에 플라스마 내에서 반응성 질소의 분해속도를 낮추어 가스 상태의 핵 형성에 의한 먼지입자의 생성율을 낮추기 위해서다. SiH4/N2O 혼합비율은 박막의 굴절률 특성을 상당히 변화시키는데, N과 Si 함유량이 클수록 굴절률은 증가하게 된다. 대체로 PECVD SiO2 박막은 압축 응력을 갖고 있으나, 입력 파워의 주파수를 바꾸면 인장력(tensile stress)으로도 바뀔 수 있다. |

| Fig.12 증착된 박막의 Stepcoverage 특성 (a) 증착 입자의 빠른 표면 이동에 의한 Conformal coverage (b) 긴 평균 자유 행로와 표면 이동이 없을 때 nonconformal coverage (c) 짧은 평균 자유 행로와 표면이동이 없을때 nonconformal setpcoverage |
|
|
균일한 표면 덮음율(Conformal stepcoverage)는 [그림12]에서 보듯이 측면이나 바닥의 박막두께가 일정한 것을 의미한다. 이것은 표면에 흡착된 라디칼이 반응하기 전 표면을 따라 빨리 이동하여 균일한 표면농도를 유지하기 때문이다. 만일 라디칼의 표면 이동이 없으면 증착속도는 입자들의 입사각도에 의존하게 되는데 가스의 평균자유행로가 단차의 길이보다 길면 상단의 입사각도는 180도이나 바닥 면의 입사각도는 90도가 되어 바닥 면의 증착속도가 떨어진다. 또한 평균자유행로가 더 짧을 경우 상단의 입사각도는 270도가 되나 바닥 면은 90도가 되어 더욱 악화된다. 이러한 관점에서 PECVD는 APCVD보다 평균자유행로가 길어 더 좋은 표면 덮음율을 갖게 된다. PECVD SiN 박막은 알칼리 금속이나 수분에 대한 침투억제능력을 갖고 있고 SiO2 박막은 전자이동을 막아주는 특성을 갖고 있어, 이 두 가지 박막을 동시에 금속배선 보호막으로 사용한다. |
|
⊙ PECVD W, WSI2 박막 |
텅스텐(W) 박막 증착은 WF6/H2 혼합가스를 이용해 생성한다. 증착 속도는 박막의 활성화 에너지와 관련이 있는데, PECVD의 활성화 에너지는 0.16 eV로 APCVD(0.69 eV), LPCVD(0.71 eV)와 비교할 때 매우 낮고, 또한 APCVD의 경우 증착속도는 기판의 표면에서 H2 분해율에 의해서 결정되는데 비해 PECVD는 수소원자가 플라스마 내에 이미 존재함으로 200-400℃ 정도의 낮은 온도에서 높은 증착속도를 보인다. 이와 같이 증착된 W 박막은 구조적으로 열적(columnar) 구조를 갖고 있으며, 200 nm 두께에서 20-40 nm 크기의 낟알(grain)은 후속열처리(900 ℃)공정에 의해 50-70 nm 정도까지 성장되어 저항이 낮아진다. 또한, W 박막의 저항은 가스조성비, 기판온도 등에 의해 조절되기도 한다. WSi2나 MoSi2는 디바이스가 고 집적화(1 DRAM 이후) 되어 종래 게이트 전극으로 사용되어 왔던 폴리 실리콘의 면저항(sheet resistance)이 높아 디바이스의 속도를 저하시키는 문제가 크게 대두되어 본격적으로 도입되었다. WSi2는 WF6/SiH4 혼합가스에 의해 생성할 수 있는데, 플라스마에서 Si를 공급, 표면에서의 쉬운 핵 형성으로 W 박막의 증착 속도보다 WSi2 증착 속도가 더 빠르다. 이 박막의 W와 Si의 조성비와 비저항은 일반적으로WF6/SiH4 가스의 혼합비율에 의해 제어되며, 박막에 함유된 F와 H의 결합이 저항을 높이는 요인이 됨으로 열처리를 하여 이들을 박막에서 방출시켜 저항을 낮추어야 한다. |